Uniform Crystal Temperature Sensors
www.lgtechlink.com
Uniform Crystal Temperature Sensors (UCTS)
How It Works
UCTS is an innovative temperature measurement technique based on the phenomenon of irradiation induced SiC crystal lattice expansion,followed by the relieving of the expanded lattice structure during the annealing process.
In the following model spheres are used to represent individual atoms, which when grouped together make up the Crystal Lattice.Numerous parallel planes can be drawn through the high concentration of the atoms; all of these planes will reflect XRays. The distance between these planes is called D-Spacing and is an important characteristic of each crystal lattice. Irradiation creates “Point Defects”which increases lattice volume (D-spacing). Annealing at T > Tirradiation has the opposite effect on a crystal lattice.
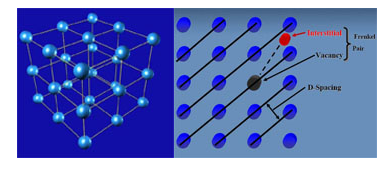
Resulting value of D-spacing after the engine test depends on:
- Temperature level (strong function)
- Duration of annealing (log dependency)
Recorded Time History (i.e., normalized reference temperature vs time of testing) is used to calculate the Equivalent Time, and subsequently Tmax of annealing.
Features
Temperature Range | 150 -1450 [deg.C] |
Size | 0.2 x 0.2 x 0.38 [mm] |
Average Accuracy (Standard Deviation) | ±3.5 [deg.C] |
Lead wire / Connectors | Not Required |
Shelf Life | Unlimited |
Test Profile Restrictions | None |
Radiation / Chemical Hazard | None |
Bebefits
- On Rotating Parts
- In places where it is difficult to get access to
- Where a high density of instrumentation is needed
- Cost effective
Application case:
Siemens used UCTS in its SGT-800 Development
- 1,975 Crystal Sensors used to map engine hot section.
- 90 sensors placed on a single blade to achieve the density of instrumentation required for the validation of 3D computational tools.
- 95% of sensors survived the test.
- Design Modifications made on the basis of this test data allowed Siemens to reduce the amount of cooling air by more than 25%.
- Reduction of thermal gradients at critical locations improved Thermo-Mechanical Fatigue characteristics.
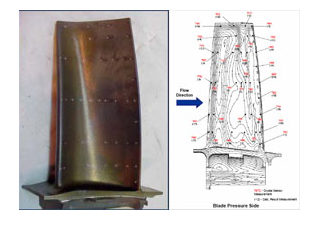