Optical Dynamic Pressure Trans
http://www.oxsensis.com
Dynamic Pressure Sensors at Temperatures > 1,000 °C (1,800 °F)
Oxsensis 1,000 °C Dynamic Pressure Sensors
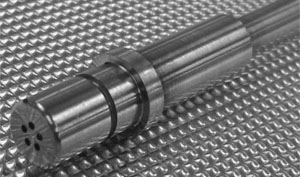
As limits imposed on exhaust emissions levels are tougher, gas turbine manufacturers are being driven to further improve their lean-burn or dry-low NOx combusting systems. This drive has pushed the fuel-to-air ratios in these combustion systems to ever-lower levels, consequently bringing the flame very close to its stability limit. Under these operating conditions, the system is more vulnerable to large pressure pulsations and may experience problems such as acoustic resonances, flamingout or flashback, that can seriously damage components both in the combustion system itself and also further downstream.
As the drive to higher efficiencies continues, designers wish to increase firing temperatures further, and that will push stability issues even closer to the edge.
To cope with it, beginning from 2008, U.K. sensor developer Oxsensis started launching the Wave-Phire series of sensors, the world’s first commercially available 1000°C dynamic pressure sensor products designed for use at extreme temperatures that are immune to electromagnetic interference (EMI) effects common in turbo-machinery such as gas turbines.
The first of the new family is the Wave-Phire DP series. They are actually dynamic pressure sensors capable of operating up to 1000oC. The system has been used in several full-scale gas turbine trials, as well as in combustion rigs up to 1000oC and has shown measurement capability, repeatability, and survivability. Further development of the range has extend the measurement capability to allow dynamic and static pressure, and temperature from a single sensor head, as far hotter locations than has previously been possible with conventional sensors.
Unlike traditional piezoelectric-based dynamic pressure sensors, the Wave-Phire sappire sensor can be flush mounted to the combustion chamber rather than being set back from the chamber or even held away from the engine.
Testing personnel benefit from being closer to the combustion chamber more than any other sensor, including the fact that it can reliably measure a much larger bandwidth. Besides, since long impulse/pressure lines are no longer needed, the associated attenuation or amplification are no longer a concern. Furthermore, there are no leak paths associated with the long impulse/pressure lines and the connectors used in these designs.
There are other benefits: no lag in response time from being held away from the chamber – multiple sensors can therefore be used to understand the phase of acoustic waves. Also, the high temperature capability means that no cooling air, either from engine bleed or “shop air”, is required to cool the sensor – making the system far easier to operate.
The improvements to the measurement capability in the combustion system will allow development teams to capture the best possible data for design improvements.
The sensor head is interrogated using an optical technique to extract the data from the sensor response and this is then fed directly into a dedicated data-monitoring system. The fiber optics at the core of this system also gives it immunity to the effects of EMI.
In the area of condition monitoring, the sensor system can be coupled with Oxsensis’s in-house monitoring software suite, S-Phire, that will allow the data to be trended and alarm levels for multiple frequency bands to be defined by the user. The operator will then receive an early warning of imminent pulsations and this allows a preventive and proactive stance to be taken on engine operation and maintenance.
The company added that future versions of the i-Phire interrogation system will enable the same single sensor head to measure both dynamic and static pressure simultaneously and also allow self-temperature measurement, further enhancing the data available for improving the operating efficiencies and for monitoring the engines’ health.
As part of their ties working in the gas turbine industry, Oxisensis is one of 17 European organizations working together on HEATTOP, a gas turbine program. Other collaborators in the three-year program include Siemens AG and Rolls-Royce, as well as Oxford and Cambridge Universities. The US$11 million program, backed by the Commission of the European Communities, aims to advance technologies available for gas turbine life optimization, performance and condition monitoring through accurate high-temperature engine measures.