Radio Telemetry
http://www.sensortelemetrie.de
Radio Telemetry
Manner Radio Telemetry
Mananer Sensortelemetrie specializes in non-contact sensor digital data transmission for industrial applications. It offers solutions for problems related to non-contact, bi-directional sensor data transmission involving rotating or moving parts.
What is telemetry
Telemetry is the non-contact bi-directional transmission between a moving part (especially a shaft) and a stationary point via a modem, with simultaneous energy transmission.
More
Benefits of Telemetry
Due to the special patented transmission technique of absorption modulation, our systems can be used under the highest EMC load. Even if they are installed in GTO-controlled large-sized motors with a power of 50 Megawatt or more, there is no interference in the signals.
More
Major Parts of Telemetry System
MANNER's Telemetry System consists of the following parts:
1. Sensor Signal Amplifier
2. Multi-Channel Techniques
3. Sensor
4. Various Transmission Possibilities
5. Evaluation Units and Interfaces
6. RMC Technology
7. Sensortelemetry with Radio Transmission
APPLICATIONS
Manner's Telemetry Systems have been successfully applied in the following areas:
- Automobile Drive Trains
- Automobile Engines
- Aviation Rotor Test Stands, Turbines
- Navigation, Geological Bores
- Industrial Applications
- Applications with Explosion-Protection Requirements
- Railroad
- Windenergy
More
Torquemeters Are also Available with MANNER Based on Sensor Telemetry Technology
High Speed Torquemeters Based on SensorTelemetry
- Gasturbines
- Helicopter Test Rigs
- Jet Turbines
- Speed:0 to 45000 rpm
- Load Monitoring
- Nutrunners
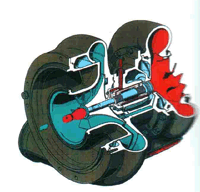
Telemetry is the non-contact bi-directional transmission between a moving part (especially a shaft) and a stationary point via a modem, with simultaneous energy transmission.



Mananer Sensortelemetrie specializes in non-contact sensor digital data transmission for industrial applications. It offers solutions for problems related to non-contact, bi-directional sensor data transmission involving rotating or moving parts.
- Customized telemetry systems for customer-specific applications
- Customized rotating torque transducers for test stand and industrial applications
- OEM-based, low cost torque transducers
- Low-cost, customized transmission systems for series production
Due to the special patented transmission technique of absorption modulation, our systems can be used under the highest EMC load. Even if they are installed in GTO-controlled large-sized motors with a power of 50 Megawatt or more, there is no interference in the signals.
The consistent monitoring of signal transmission allows you to achieve a high degree of reliability: incorrect assembly of antennas, faulty sensors, insufficient energy supply or defective cables are detected immediately and displayed.
MANNER systems were developed for use under the toughest ambient conditions and are characterized by sturdy solder pins, casing (which ensures oil-tightness) and extreme acceleration stability (up to 120,000 g). They can be supplied according to the requirements of the IP67 protection class.
Technological features at a glance:
- Miniature rotor electronics with very small dimensions (7 x 25 x 6 mm) and low weight (2 g)
- Extremely high interference immunity due to the use of the patented sensortelemetry technique.
- Acceleration stability up to 120,000 g and speed stability up to 100,000 rev./min
- RMC technology (remote-controlled online conditioning of measuring amplifiers, amplification and zero point with 16 bit resolution), autozero in the rotor
- Frequency modulated (FM) and pulse-code modulated (PCM) transmission technique
- Digitization in the rotor
- Highest sample rate of up to 400 kSample/channel (simultaneous transmission of 52 measuring channels)
- With Flex technology, the sensor signal amplifier can have any geometrical shape and can therefore be installed even if the installation space is not ideal.

1. SENSOR SIGNAL AMPLIFIER
- Stability with regard to ambient conditions (oil, water, etc.)
- Acceleration stability
- Robustness
- Temperature stability
- Drift characteristics
- Measuring accuracy and resolution

Due to the different shapes and sizes of the housing, it can be adapted to most applications. Thanks to the use of sturdy solder pins, a reliable connection
to the sensors is ensured even under severe ambient conditions.
Miniature models
Space requirement is a deciding factor for the use of telemetry. That is why Manner started focusing on the development of miniature sensor signal amplifiers at a very early stage.
As a result of our consistent miniaturization efforts, today we can provide single channel sensor signal amplifiers with a size of only 7 x 25 x 6 mm and a weight of 2 g!
Flex technology
Thanks to a specially developed flex substrate (installation height <2.5 mm), the sensor signal amplifier is flexible and can be wound around the shaft and then encapsulated.
The smallest bending radius is 8 mm. This technology opens the door to previously unimaginable applications involving input shafts, toothed wheels, universal shaft transmitters,
injection pumps etc.
THE RIGHT TRANSMISSION TECHNOLOGY WITH DIGITAL TRANSMISSION
Although the time-tested analog technique with FM modulation is still used, today we mainly use digital transmission techniques for inductive as well as radio transmission.
This offers the following advantages
• Minimum temperature drift < 0.002 %/°C in the measuring range 1 mV/V
• High temperature stability up to an ambient temperature of 180°C
• High transmission speed under EMC conditions
• Additional increase in transmission safety through CRC (checksum) data storage
• No cross-talk with multi-channel technology
• High data rates and number of channels (200 kSample/sec/channel) with simultaneous use of 48 channels
• High resolution (max. 16 bit)
• Simultaneous transmission of up to 100 measuring channels (sample rate of 200 kSample/channel/sec)
• Sample rates up to 400 kSample/channel/sec
• Max. total data rate 200 Mbit/sec
• Externally synchronized sampling
• No cross-talk due to digital multiplexing
• Separate supply voltage for individual sensors
• Optional scanner operation - up to 1000 measuring channels
• High temperature stability up to 180°C
• Acceleration stability up to 100,000 g
• Integrated data storage CRC
• Remote conditioning of measuring ranges
• Modular design (distributed arrangement, bus technology)


All sensor cells without integrated measuring amplifier available in the market can be directly switched on. This saves power in the rotating system and, therefore, reduces costs.
All standard sensor signal amplifiers can directly process all strain gage bridge models or sensors with voltage or current output as well as PT100 and thermocouples. For ICP, piezo-electric, µ-[1]-, and LVDT sensors, special speed and temperature stable input modules are available which are usually integrated in the sensor signal amplifier.
Naturally, supply to active sensors is also taken care of via sensortelemetry.


Since telemetry normally constitutes only a part of the entire measurement recording system, it is very important to integrate it seamlessly.

Our systems are equipped as standard with the following features:
• With FM systems, optionally with a 10 kHz ±5 kHz frequency interface, TLL level
This is why digital interfaces are becoming more and more important.
The following interfaces are available:
• CAN serial interface
• RS232 serial interface
• High-speed 16-bit parallel interface (max. 30 Mbyte/sec)
Plug-in Card for MGC
For single channel systems, a plug-in card is available for the Hottinger MGC. It allows you to directly connect telemetry channels to Hottinger detection systems.
MANNER Sensortelemetrie was the first to introduce remote-controlled measuring range selection, which is available for both single and multiple channel systems. Due to consistent further development, today it is possible to set digital systems with 16 bit resolution, zero point and amplification almost infinitely on the sensor signal amplifier. In other words, the entire adjustment is performed online in the rotor on the input amplifier. The setting range for sensitivity is between 0.05 mV/V and 20 mV/V and for zero point between 0 and 2.5 mV/V. Data transmission occurs via the bi-directional telemetry line.
Significant advantages:
• No solder resistors
• Infinite measuring range selection and zero point adjustment online during the measurement without mechanical access to the rotor
• With a standardized output signal at the sensor signal amplifier, various sensor signal amplifiers can be operated with an evaluation unit without loss of calibration.
• Error-free measurement through direct input of the physical parameter (torque, force...)
• Electronic amplifier detection with serial number identification
RMC-Technology - (not only) a matter of comfort
In many cases, the expected signal values can be estimated only to a limited extent. For example, installation in a gear involves a lot of assembly work and high test stand costs. Without the RMC function, an incorrectly selected measuring range means the gear and the sealed amplifier must be opened again, the rotor electronics must be readjusted - a task requiring a lot of effort - and then the units must be assembled again.
How does the RMC technique work?
The sensor signal amplifier has a programmable amplifier whose input offset and amplification are digitally adjustable. An integrated processor supplies the necessary data to the amplifier and decodes the data transmitted via the telemetry line. This data is saved in a permanent storage and is therefore immediately available even if there is a power failure or if commissioning must be performed again. The conditioning data is stored in the sensor signal amplifier until new data is entered; the new data is generated at the stationary end. With a program, the measuring range and the zero point (in mV/V) can be set in a userfriendly manner via a PDA or laptop. Display of the current measured values and automatic zero point setting are standard features..
Adjustment in the rotor with RMC technology
In order to optimize accuracy and resolution, it is necessary to use the entire control range of the telemetry channel. This is possible only with optimized adjustment of the measuring range and the zero point. Since the sensor signal values at trial parts vary to a large extent (20 µV to 100 mV), the conventional method of adjusting the amplification and the zero point with resistors is extremely time-consuming, especially in case of small signals. Another problem is the speed-stable installation of resistors.
RMC technology in half shafts
Due to the rough testing conditions, half shafts in passenger cars must be enclosed, which is a very complex task. In the course of production, calibration is the last step. With RMC technology, settings for enclosed shafts can be performed during the calibration process. Incorrect calculations of balancing resistances are a thing of the past; later corrections can be performed without opening the enclosure. A zero point offset caused due to plastic deformation of the shaft during a start-off maneuver can also be easily corrected.
Multi-channel system and RMC technology
With a 25-channel sensor signal amplifier, every channel must be separately adjusted. Due to the frequent demand for compact design and the large number of connected sensor wires, soldering of measuring range and zero point resistors is a real challenge. Even if only one channel has to be changed, this usually necessitates a time-consuming re-instrumentation, which is further complicated by the speed-stable enclosure. You don’t have these problems with RMC technology since every channel can be conditioned at any time - even during the measurement - from the laptop.
7. SENSORTELEMETRY WITH RADIO TRANSMISSION
Preferred applications:
• Wheel measurements on the vehicle with the goal of avoiding disturbing supply lines
• Measurements on large shafts (< 1 m; cement mills, wind power mills)
• Shafts with large movements under load (> 50 mm; train drives)
• Force measurement at conveyor chains
How does sensortelemetry with radio transmission work?
Whereas inductive sensortelemetry works with an inductive interface, sensortelemetry with radio transmission works with a radio interface. The time-tested PCM technique, which is characterized by the highest interference immunity, is used as the modulation technique. The transmission is purely digital (PCM technology) with 12 or 16 bit resolution. The highly accurate measuring amplifier cells are identical to inductive systems; handling, measurement accuracy and adjustment of the sensor signal amplifier are as usual. RMC technology (programmable measuring range setting) is also available. MANNER sensortelemetry with radio transmission was specially developed for severe condition use in measurements with demanding ambient conditions.
Radio interferences?
A radio transmission line is susceptible to interferences, multiple-path reception, fading, EMC and location-dependent signal zeroizing. With the special MANNER data transmission safety protocol (CRC), transmission errors are detected and suppressed 100 % so that it is not necessary to correct the measured values later.
Due to the use of 2 receivers with antennas at various locations and a downstream diversity combiner, the reception in a high interference environment can be improved by a factor of up to 1000. The diversity combiner selects the error-free data signal from the two receiver signals. Especially in case of large shafts with rotation angle dependent shading, interferences, multi-path reception and fading, the measurement signal transmission can take place with almost no loss of data.
Sensortelemetry with radio transmission is particularly advantageous for short-term measurement on rolling roads, rotary furnaces and cement mills. Unlike conventional radio technology, antenna diversity ensures that there is neither any disturbance nor loss of data even in case of shading and fading.
Radio LAN technology
With radio LAN technology, measurement signals of locally distributed sensor signal amplifiers (e.g. vehicle with 4 test rims) can be detected with one receiver and digitally transferred to the measurement recording system via CAN. All LAN sensor signal amplifiers
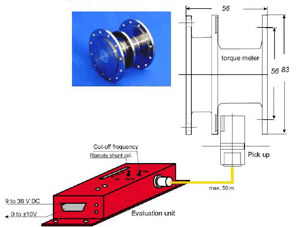
1. DRIVE TRAIN, AUTOMOBILE
Today, sensortelemetry has become an indispensable tool for automobile developers in order to design and optimize the drive train.
or gaging due to integrated shielding and automatic balancing.
- Torque measurement in prop and half shafts with strain gage measuring bridge, sensor signal amplifier and rotor induction loop with radially
inductive transmission encapsulated for operation under the toughest conditions (IP67).
- Divisible inductive transmitters with integrated sensor signal amplifier in prop and half shafts for simple assembly.
- Wheel torque transducers for the most demanding requirements, based on sensortelemetry with radio transmission with integrated
overload protection
- Wheel telemetry Single/multi-channel radio transmitter for temperature measurement of brake disks or torque measurement in half shafts
- Torque measurement at input shaft (gear input). Special feature: no weakening of the shaft. The installation height of the electronic system
is only 2.5 mm
- Highly precise measurement of the dynamic torque between the engine and the gear via modified flexplate with 0.1% accuracy.
Temperature range -30 to 160°C
- Temperature measurement at the multi-disk clutch in the automatic gearbox.
- Universal shaft transmitter for prop shaft with integrated sensor signal amplifier (splash water resistant).
- Divisible universal shaft transmitters with integrated sensor signal amplifier and speed measurement
(characterized by quick installation, particularly for examination of third party vehicles).




Plug and Play Universal Shafts Divisable Transmitter Universal Shaft Transmitter

Input Shaft
we were able to considerably increase the power density and the efficiency over the past years.
transmission of all data collected during a piston stroke to be transmitted during the short signal contact time. This makes the application of such
a complex system very easy since hardly any machining is required for the engine parts.
- Real time measurement of the contact forces of the highfrequency torsion and bending vibration at the fired racing motor F1.
- With our high temperature technology, today it is possible to measure the temperature at the piston online for all operating states when the engine
is fired. The measuring amplifiers, which are temperature-stable up to 180°C receive a signal from robust thermocouples. The measured
temperature values are transmitted once per piston stroke. The transmission elements are extremely compact and can be easily mounted
on the piston with minimal mechanical modifications.
- Valve telemetry for unfired operation in order to measure the dynamic forces in the shaft during various engine operating states.
- The measurement of dynamic chain forces during circulation in various operating states of the engine provides help in designing
the chain tensioners and reducing noise and wear. Signal bandwidth 0 to 40 kHz at an ambient temperature of 150°C.
- Torque measurement at crankshaft pulley for determining the energy requirement of the auxiliary units and reaction of the auxiliary units on engine operation.
- Torque measuring shaft for turbo charger (max. 100,000 rev./min)
- 8-channel sensortelemetry with axial coupling, real time measurement of the dynamic bending moment/torque development and axial movement of the con rod.
- Sensortelemetry is indispensable for optimizing the turbo charger (blade vibrations, temperature distribution).




Piston Temp. Measurement Valve Head Measurement Airconditioning compressor Auxilary Unit

Chain Telemetry
3. AVIATION, ROTOR TEST STAND TURBINES
There are a number of applications in the area of aviation. This does not only apply to tests.
- Also offered is a mast monitoring system for helicopters which is based on sensortelemetry for series production. Almost every German helicopter has a MANNER system on board. It was possible to achieve this qualification
only because of the high quality of our products.
- Today, sensortelemetry is an important tool also for Airbus. Sensortelemetry is used for component testing in several Airbus models (A380, A350, A400 etc.). In these applications, a large number of systems are used in a very
limited space without any interference problems.
- A special highlight is the MANNER turbine telemetry system. Unlike other systems, it works absolutely simultaneously. All measuring points (up to 100 dynamic channels (bandwidth 5 to 50 kHz) and up to 300 temperature
measuring channels) are covered simultaneously - a significant advantage compared to the multiplex technique.



In the area of drilling technology, too, sensortelemetry is used under the roughest conditions (ex) and offers significant advantages for online measurement of the drilling moment, the feed force and the deflection forces which act during drilling. Even the high continuous temperatures of 150°C at a depth of 5000 m are no problem.


SCHOTTEL twin propeller STP Guided Bore
5. INDUSTRIAL APPLICATIONS
Typical Applications:
- Early detection of damage of automatic door closures
- Monitoring of the load on gears (estimation of remaining life)
- Rotor temperature monitoring in largesized motors/generators
- Shaft power measurement in turbo compressors
- Nut torque monitoring in robot running spindles



stand applications with thermocouple
and strain gage


Typical applications:
- Viscosity measurement
- Agitator monitoring
- Data transmission from high/ low pressure areas
- Polishing devices with inflammable materials
- Feed rate measurement (torque, pressure, temperature)




Test Stand Measuring Flange Test Stand Machine Monitoring

Machine Monitoring
7. RAILROAD WINDENERGY



Brake test stand - test stand Power Measurement Power Measurement
for train brakes with sensortelemetry

APPLICATIONS
- Gasturbines
- Helicopter Test Rigs
- Jet Turbines
- Linearity(incl.hysterese):0.1%
- Temperaturedrift:0.03%/10K
- Axial Length:56mm
- Max.staticbbreaking load:400%
- Stiffness: 0,02degree(norminal)
- Admissible Longitudinal Force:7,5N/Nm(nominal)
- Protectiontype:IP65
- Signal Bandwidth:0 to1kHz(40kHz)
- Temperature Range:-30°C to 85°C (max.140°C)
- No maintainance
- Contactless
- Low Inertia (depending on range)
- RPM Signal (Option)
- Type:MHSP_<range>_<signalbandwidth>_0.1_<temp>
APPLICATIONS
- Load Monitoring
- Nutrunners
- Speed:0to30000,(100000)rpm)
- Linearity(incl.hysterese):0.2%
- Temperature drift:0.03%/10K
- Lenth:axiallength:85mm
- Nominial diameter:15mm
- Max.static breaking load:400%
- Stiffness:0,02degree (norminal)
- Admissible longitudinal force:7,5N/Nm(nominal)
- Protectiontype:IP65
- Signalbandwidth:0 to1kHz(10kHz)
- Temperaturerange:-40°Ct o 85°C (max.140°C)
- Nomaintainance
- Contactless
- Very low inertia (depending on range)
- RPM signal (Option)
- Type:MMM_<range>_<signalbandwidth>_0.1_<temp>
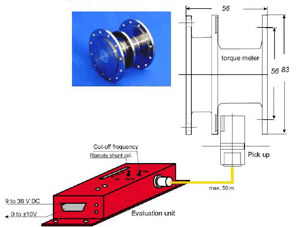