Fiber-Optic Sensors
https://www.hoodtech.com/
High Temperature Fiber-Optic Sensors for Blade Vibration Monitoring
Fiber-Optic Blade Tip Sensors
Hood Tech builds optical sensors in a range of sizes and temperature capabilities. Temperature limitations of the sensors are dictated by the optic fibers. Using high-temperature fibers, temperatures of up to 650C can be tolerated. With a small cooling manifold air-cooled optical sensors have been used to 1100C successfully. The most common sensor size of this type built by Hood Technology Corporation is shown in the following figure.
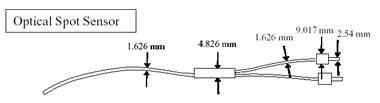
Distance (inch) |
Gas Temperature Up To |
Extension Cable
|
|||||
700°F | 1200°F | 2500°F | |||||
Type |
Diameter (inch) |
Type |
Diameter (inch) |
Type |
Diameter (inch) |
||
Blade Time-Of-Arrival Sensor | |||||||
0 - 0.020 |
MiniOpt100 - 1F/700
|
0.005 | MiniOpt100 - 1F/1200 | 0.005 | 100-1F | ||
0 - 0.040 | MiniOPT200 - 1F/700 | 0.010 | MiniOPT200 - 1F/1200 | 0.010 | 200-1F | ||
0.030-0.300 | MiniOPT200 - 7F/700 | 0.045 | MiniOPT200 - 7F/1200 | 0.045 | MiniOPT100 - 7F/2500 | 0.130 | 200-7F |
0.125-0.750 | LineOPT200 - xF/700 | NA | LineOPT200 - xF/1200 | NA | LineOPT200 - xF/2500 | NA | Line-xF |
Blade Tip Clearance and Blade Time-Of-Arrival Sensor | |||||||
0.020-0.300 | MiniOPT - SDLP/700 | 0.125 | MiniOPT - SDLP/1200 | 0.125 | Two 200-7F |
Eddy Current Blade Tip Sensors
Hood Tech builds eddy current sensors in a range of sizes and temperature capabilities. Such sensors can be used in temperatures up to 550C uncooled. In turbines, such sensors have been operated successfully with cooling airflow routed through the sensor in 1mm steel tubing, maintaining the sensor’s interior below 500C. This approach has been applied with gas temperatures in the stage being measured as high as 1000C.
The most common sensor size of this type built at Hood Technology is show in the following figure.
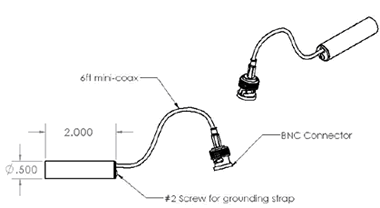
In addition to a large number of gas turbine engines, this sensor has also been used with success in steam turbines, in each case on the final few stages of the LP turbine. For these steam turbine applications, the sensor housing is made with an erosion resistant material. Several eddy current sensor installations have been in continuous operation for over 2 years in gas turbine engines and steam turbines with no degradation in signal quality.
Distance (inch) |
Gas Temperature Up To |
Extension Cable
|
|||||
350°F | 900°F |
2000°F, Higher temperatures will be subject to sensor head diameters |
|||||
型号 |
直径 inch |
型号 |
直径 inch |
型号 |
直径 inch |
||
0 to 1/2 of sensor head's diameter |
Eddy-TTC/350 Eddy-STD/250 |
Above 0.250 |
Eddy-TTC/900 Eddy-STD/900 |
Above 0.250 |
Eddy-TTC/2000 Eddy-STD/2000 |
Above 0.350 |
Standard BNC |
The principle of eddy current sensor operation is to create a permanent magnetic field through which the rotor blades pass, disturbing the field. If the blades are electrically-conductive (not necessarily ferrous), rapid eddy currents in the passing blade, disturb the permanent magnetic field. This field disturbance is sensed by a coil within the probe. We have used such sensors to 550C uncooled. In turbines, we have operated such sensors with cooling airflow routed through the sensor in 1mm steel tubing, maintaining the sensor’s interior below 500C. We have used this approach with gas temperatures in the stage being measured as high as 1000C.
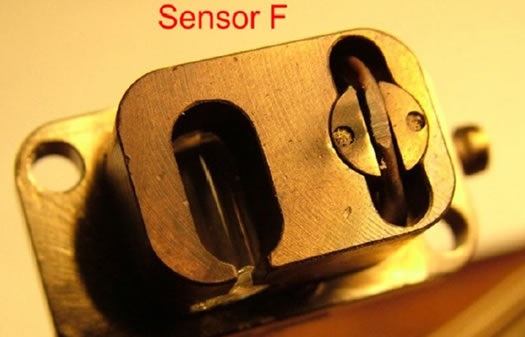